Certified Repair Process
Honed from over four decades of experience, our DC torque tool repair process at K+S is designed to restore precision and reliability to your tool lineup.
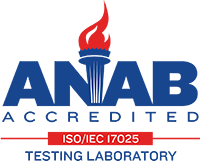
Torque Accuracy Evaluation
Checking for calibration drift and torque delivery inconsistency.
Tool-Specific Disassembly & Inspection
Focusing on gearboxes, motors, and control interfaces.
Detailed Cleaning & Component Assessment
We ensure integrity of internal mechanisms and electrical components.
Precise Repair & Calibration
Restoring tools to manufacturer-specific torque settings.
Functional Testing Under Load
Confirming tool accuracy and operational reliability.
In-Depth Torque Tool Failure Analysis
We offer insights on mechanical wear and electronic faults to head off future repair costs.
Experienced Assembly Tool Technicians
We have experience working on a wide variety of DC torque tool types, from nutrunners to torque and angle wrenches.
Commitment to ISO 9001 Standards
Ensuring each repair meets rigorous quality criteria.
Brands
We service a range of DC torque tools from leading brands like Atlas Copco, Stanley, and more. Contact us to learn more about the brands we work on.
- Atlas Copco
- GSE (CP Tech-Motive)
- FEC
- Cooper Cleco
- Ingersoll-Rand
- Rotor Tool
- Stanley Tool
- Gardner-Denver
- Estic/Cinetic/Tayio
Does My DC Torque Tool Need Repair?
Your DC torque tool may need repair if it shows:
- Inaccurate torque delivery.
- Unusual noises or vibrations during operation.
- Electrical or calibration issues.
- Physical wear or damage.
Still not sure if your tool needs repair? Talk to a K+S expert today about whether your torque tools need service.