Certified Repair Process
K+S has been a leader in industrial repair for over 40 years, and our ISO 9001 certification underscores our commitment to quality and customer satisfaction. Our hydraulic repair process has been honed to ensure the highest standards.
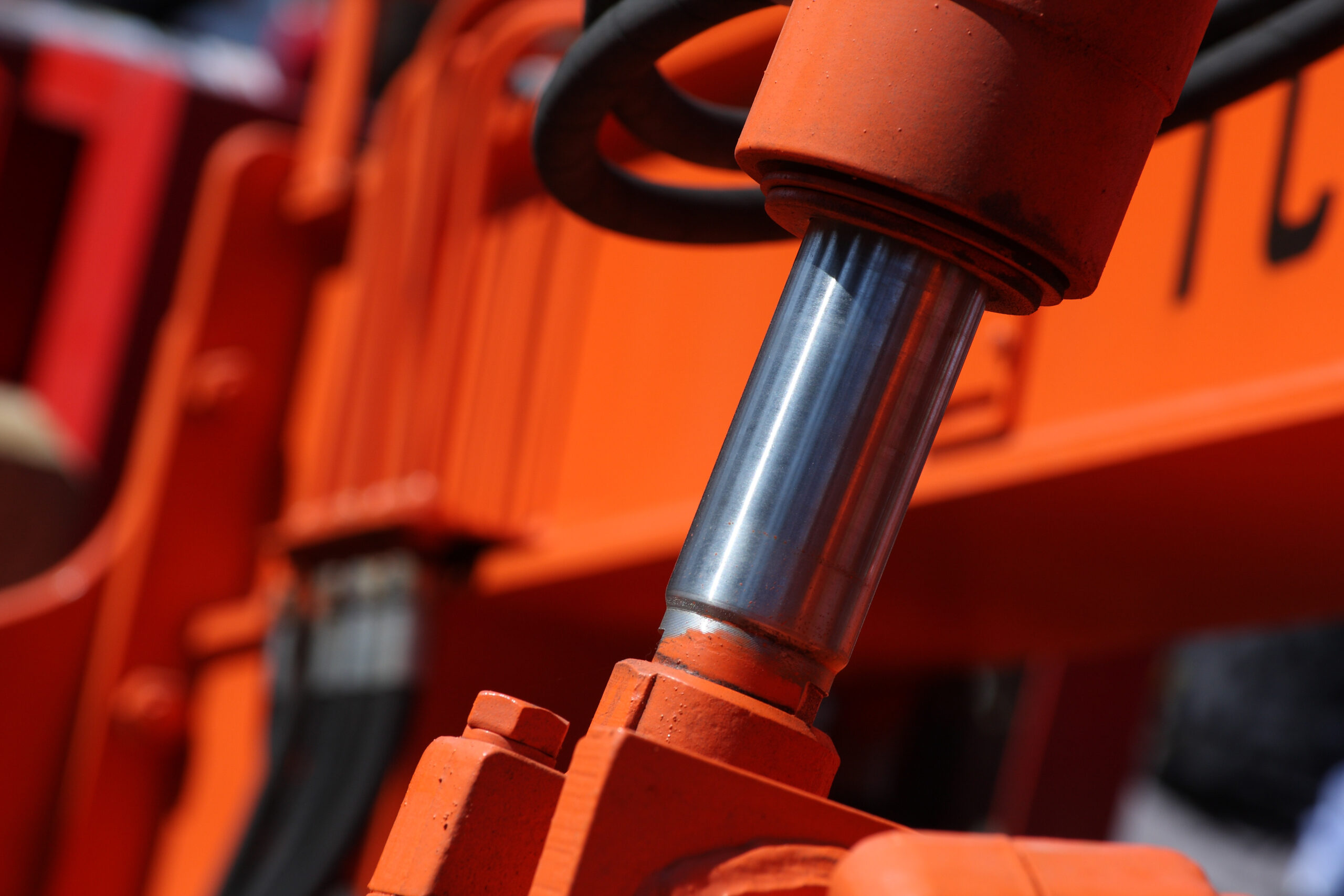
Free Evaluation
We begin with a comprehensive assessment to identify the root causes of any issues.
Component Disassembly
Our skilled technicians carefully dismantle each component for a detailed inspection.
Thorough Cleaning & Inspection
Every part is rigorously cleaned and inspected to ensure it meets our high standards.
Detailed Part Repair or Replacement
We use only OEM or equivalent parts for repair or replacement, adhering to strict quality guidelines.
Rigorous Testing
Post-repair, each component is tested under load conditions to confirm it meets or exceeds OEM specifications.
Failure Analysis Reporting
Our detailed reports provide insights into the causes of failure, helping prevent future issues.
Experienced Technicians
Our team, with decades of expertise, ensures that every repair is conducted with precision and care.
Quality Assurance
Adherence to ISO 9001 standards throughout the repair process guarantees a reliable and high-quality service.
With our extensive experience and commitment to quality, K+S is equipped to handle the most challenging hydraulic repair needs, delivering solutions that keep your operations running smoothly.
Brands
We service a wide range of hydraulic components from Bosch Rexroth, Parker, Vickers, Moog, and many other brands. Contact us to find out more about the brands we service.
Does My Hydraulic System Need Repair?
Your hydraulic system should be professionally repaired if it has:
- Unusual noises like whining or banging.
- Slow or sluggish operation.
- Visible fluid leaks or drops in fluid levels.
- Erratic system behavior or decreased performance.
Want to discuss a specific piece of machinery or get more information about our hydraulic repair service? Contact a K+S expert today.